Ja, megkezdődött az új 7-es BMW sorozatgyártása (2.)
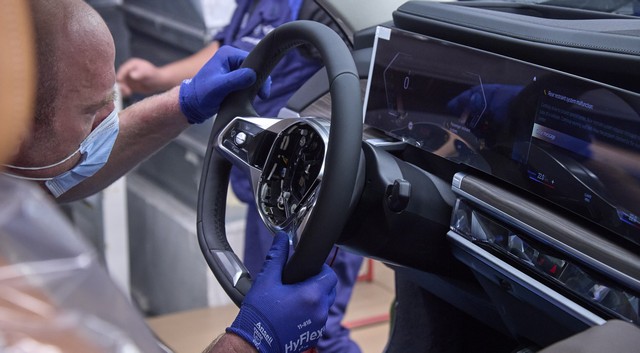
A hálózatról tölthető hajtáslánc-technológiák házon belül készülő alkatrészei
A BMW i7 hajtáslánc-technológiájának főbb alkatrészei – kiváltképp a nagyfeszültségű akkumulátor és a nagymértékben integrált tisztán elektromos meghajtás – ugyancsak Dingolfingban készülnek, nem messze a sorozatgyártást végző gyártósoroktól. Ezek az alkatrészek a BMW Group hálózatról tölthető hajtáslánc-technológiákra szakosodott kompetenciaközpontjában látnak napvilágot, a BMW iX, a BMW i4 és a BMW iX3 hajtáslánc-technológiáinak főbb alkatrészeivel együtt.
A bajor prémiummárka dingolfingi kompetenciaközpontja nemrégiben két új gyártósort állított rendszerbe, amelyeknek köszönhetően a létesítmény immár évente több mint 500 000 darab hálózatról tölthető új autó szükséges hajtáslánc-technológiai alkatrészeit tudja legyártani. A kompetenciaközpont 2020 elején mindössze 600 fős állománya eközben mára több mint 2 300 fősre bővült.
„A BMW iFACTORY gyártási stratégia szerinti átalakulás iránymutató ütemben zajlik”
„Úttörő technológiáiknak köszönhetően az olyan modellek, mint az új BMW 7-es sorozat, a változás valódi motorjai – miként az utakon, úgy gyárainkban is” – fogalmazott Milan Nedeljković, a BMW AG igazgatótanácsának gyártásért felelős tagja, kiemelve, hogy az új luxuslimuzin által bevezetett innovációk nem csupán magában a végtermékben, de a gyártási folyamatokban is tetten érhetők. „A BMW iFACTORY gyártási stratégia szerinti átalakulás iránymutató ütemben zajlik. Több száz munkatársunk dolgozik azon, hogy létesítményünket hatékonyabbá, rugalmasabbá és fenntarthatóbbá tegyük, olyan valódi innovációkkal és digitális megoldásokkal, amelyek a fejlődés valódi kulcsai” – tette hozzá Christoph Schröder, a BMW Group dingolfingi gyárának igazgatója.
A BMW iFACTORY gyártási stratégia „HATÉKONY”, „ZÖLD” és „DIGITÁLIS” alappillérei már ma jelen vannak a BMW Group dingolfingi gyárában.
HATÉKONY: rendkívül rugalmas gyártási struktúrák és az intelligens logisztikai megoldások széleskörű alkalmazása
A BMW Group dingolfingi létesítményének jövőbe mutató hatékonyságát elsősorban a gyártási struktúrák rugalmas elrendezése és alkalmazhatósága garantálja. „Rendkívül rugalmas gyártási struktúráink lehetőséget biztosítanak nekünk arra, hogy könnyedén váltsunk az egyes modellváltozatok és hajtáslánc-technológiák között, miközben a gyártási mennyiség tekintetében is gyorsan tudunk alkalmazkodni a folyamatosan változó igényekhez. Sőt mi több, ügyfeleink még a kiválasztott modell legyártása előtt néhány nappal is kérhetnek változtatásokat. Itt, Dingolfingban a rugalmasság mindennapi tevékenységünk szerves része” – mondta Christoph Schröder.
A dingolfingi üzem hatékonysági céljaihoz az intelligens logisztikai megoldások széleskörű alkalmazása is nagymértékben hozzájárul. A BMW Group legnagyobb európai gyára e tekintetben is iránymutató a vállalatcsoport nemzetközi gyártási hálózatában, hiszen nem csupán automatizált targoncákat és vontatójárműveket, de automatizált kimenő logisztikai megoldásokat és olyan intelligens szállítórobotokat is alkalmaz, amelyek alkatrészekkel látják el a gyártósorokat. Az új 7-es BMW sorozatgyártásának beindításával párhuzamosan 2022 végére több mint kétszeresére, várhatóan 200 fölé emelkedik a BMW Group leányvállalata, az Idealworks által legyártott és rendszerbe állított intelligens szállítórobotok száma. „Ezen rugalmas, automatizált megoldásoknak köszönhetően rendkívül hatékonyan kezelhetjük azt a rengeteg összetett alkatrészt, amelyekkel itt az üzemben dolgozunk” – tette hozzá a BMW Group dingolfingi gyárának igazgatója.
ZÖLD: befektetés a fenntartható sorozatgyártásba
A BMW iFACTORY gyártási stratégia „ZÖLD” alappillérét és a dingolfingi üzem fenntartható sorozatgyártási megoldásait számos innováció és intézkedés nyomatékosítja. Ilyen többek között a létesítmény működéséhez szükséges energia 100 százalékban zöld előállítása, a karosszériaépítő üzemben dolgozó több száz robot modernizálása és a fényezőműhely folyamatos erőforrás-csökkentése. A BMW Group jelenleg több mint 50 millió eurót fektet be a fényezőműhely új katódos merítőmedencéibe és új szárazleválasztó rendszerébe, amelyek jelentős mennyiségű vizet és energiát takarítanak meg. A szárítókemencékből származó hulladékhőt ráadásul már nem csupán technológiai hőként hasznosítják, hanem villamos energiát is előállítanak belőle.
A Dingolfingban működő gyár fenntartható termelését élteti továbbá a számos energiahatékony rendszer, a csomagolástervezés, a közlekedési logisztika, az újrahasznosítás és a vízgazdálkodás is. Az üzem területén belül elektromos teherautókkal végzik a szállítmányozást. A dingolfingi létesítmény ráadásul jelenleg több mint 90 százalékos újrahasznosítási aránnyal és még magasabb, több mint 99 százalékos újrafelhasználási aránnyal büszkélkedhet, amelyeknek köszönhetően 2021-ben az egy legyártott új autóra vetített teljes maradékhulladék-mennyiség mindössze 580 grammra csökkent. Ami pedig a vizet illeti, a dingolfingi gyár jelenleg vízszükséglete 40 százalékát saját forrásból fedezi, amellyel a régió vízkészletének megőrzéséhez is hozzájárul.
DIGITÁLIS: automatizált minőségellenőrzés mesterséges intelligenciával dolgozó kamerákkal
A BMW Group dingolfingi gyárában a termelés minden területén intelligens digitális megoldásokat alkalmaznak. Kiváltképp igaz ez az összeszerelő üzemre, legyen szó akár virtuális képzésről, intelligens szkennerekről, mesterségesintelligencia-alapú, automatizált minőségellenőrzésről vagy a frissen gyártott járművek automatizált vezetéséről.
AIQX (Artificial Intelligence Quality Next) névre keresztelt projektjével a BMW Group a mesterséges intelligencia alkalmazásának úttörőjévé érett, amelynek égisze alatt érzékelők és mesterséges intelligencia segítségével automatizálta minőségi folyamatait. A gyártósorokba épített intelligens kamerarendszerek és érzékelők valós időben rögzítik az adatokat a háttértár kiértékeléséhez, algoritmusok és mesterséges intelligencia segítségével. A visszajelzéseket a rendszer közvetlenül a gyártósoron dolgozóknak küldi el, okoseszközeiken keresztül. Az AIQX lehetővé teszi az eltérő változatok meghatározását, a teljesség ellenőrzését és az összeszerelési folyamat során esetlegesen felmerülő rendellenességek észlelését. A technológia az új BMW 7-es sorozat gyártása során jelenleg 40 alkalmazásban működik.
Az új luxuslimuzin bevezetése az IPS-i alkalmazási eseteinek számát is növelte. Ez a digitalizációs projekt egy informatikai platform segítségével konvergálja át az összeszerelő csarnokban dolgozó rendszerek széles köréből származó adatokat, amelyekből valós időben létrehozza a csarnok digitális lenyomatát. Az IPS-i platform alapot biztosít a gyártási folyamatban részt vevő összes elem – minden jármű, alkatrész és szerszám – meghatározásához és összekapcsolásához, az intelligens szkennerek és csavarhúzók használatától kezdve, egészen az alkatrészek járműhöz való hozzárendelésének RFID-alapú ellenőrzéséig. Az új BMW 7-es sorozat esetében az RFID-alapú alkatrészkövetés már 45 különböző alkatrészcsaládra terjed ki.